The blank frames made in our own carpentry workshop are further crafted in the gilding workshop and prepared for bole gilding. This can be composed of up to 15 single coatings. One differentiates between two main coatings: the mixture of finely powdered whiting and size, and the bole base.
After removing the twigs and blobs of resin, the frame is soaked in glue. The hot glue mixture made from rabbit skin glue and water opens up the pores of the wood so that the next coating can penetrate deeper into the material. This is followed by a black chalk (a soft stone substance, of a white, greyish or yellowish colour) basecoat, which is also applied warm and ensures that the next coat, the whiting (finely powdered chalk) base, adheres well. In order to achieve an ideal surface one needs seven coatings of whiting, which have to dry thoroughly. Finally the frame is smoothed down, and decoration and ornamentation are applied according to the original design. Then the preparations for the gilding work are begun. The bonding agent between the gold leaf and the whiting basecoat is the bole. Bole is a type of clay bonded with glue, and is used in the main colours yellow, red, white and black. It used to be that, in the main, one application of yellow and two of red bole were used. We have retained even till today these steps in the work process, whereby the colour hues are individually mixed in accordance with the master copy.
After the completion of the foundation, the so-called laying-on of the ten-thousandths of a millimetre thin gold leaf follows. To this end, the area of the frame to be gilded is coated with size, a mixture of spirit and water, and by means of a brush the gold leaf is carefully laid onto the “damp” frame. The size breaks down the trace of glue in the bole and after evaporation and drying respectively, the gold leaf adheres to the frame. The actual gold lustre first develops by burnishing it with an agate (a semi-precious stone), whereby the foundation is compressed and the gold achieves its deep sheen. After the frame has been gilded, a patina application gives it a natural, old look.
|
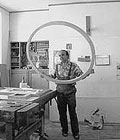 |
The Carpentry Workshop
Here craftsmanship is just as much in demand as is the competent use of spezialized machines and the knowlege of historical wood compounds.
|
View into the carpenter's workshop. In the middle of the machine room is the moulding cutter. A frame often consists of several profiles wich have to be milled seperately.
|